Boosting Efficiency with Warehouse Systems
페이지 정보
작성자 Nadia 작성일25-04-14 15:43 조회8회관련링크
본문
Warehouse automation is a rapidly increasing trend that is changing the way businesses manage their inventory and operations more effectively. By leveraging advanced technology, companies can simplify their workflow, increase efficiency, and reduce labor costs. In this article, we will explore the benefits of warehouse automation and provide strategies for enhancing productivity in warehouses.
One of the primary advantages of warehouse automation is reduced errors. With manual inventory management, human mistakes can cause discrepancies in stock levels, leading to financial losses. Automated systems, on the other hand, can accurately track inventory levels, reducing error and ensuring that stock is always available when needed.
Another benefit of warehouse automation is increased speed. Automated systems can process inventory transactions much faster than manual systems, allowing companies to fulfill orders quickly and efficiently. This can be particularly important for businesses that rely on quick shipping to stay competitive.
In addition to increasing accuracy and speed, warehouse automation can also help to reduce labor costs. By automating routine tasks, companies can reduce the need for manual labor, freeing up staff to focus on more value-added tasks. This can also help to improve employee morale, as staff are no longer burdened with unfulfilling tasks that can be automated.
To maximize productivity in your warehouse, consider implementing the following technologies:
1. Warehouse management systems (WMS): A WMS is the core of warehouse automation, providing a centralized platform for managing inventory, tracking orders, and automating tasks.
2. Automated storage and retrieval systems (ASRS): ASRS use robots and conveyor belts to store and retrieve inventory, reducing labor costs and increasing storage capacity.
3. Pick-to-light and プラスチックパレット pick-to-voice systems: These systems use lights or voice prompts to guide pickers to the correct products, reducing errors and increasing efficiency.
4. Automated conveyors and sortation: Automated conveyors and sortation systems can streamline the picking and packing process, reducing labor costs and increasing speed.
Implementation of warehouse automation requires a strategic. Here are a few key considerations:
1. Assess your current operations: Before implementing warehouse automation, it's essential to assess your current operations and identify areas for improvement.
2. Define your goals: Clearly define your goals and objectives for warehouse automation, including increased efficiency, reduced labor costs, and improved customer satisfaction.
3. Choose the right technology: Select the technologies that best fit your business needs, considering factors such as cost, scalability, and integration.
4. Train your staff: Warehouse automation requires a significant change in workflow and processes. Ensure that your staff are trained and equipped to work effectively with the new technology.
By following these best practices and implementing warehouse automation, companies can maximize productivity, reduce labor costs, and improve customer satisfaction. As the trend towards automation continues to grow, businesses that fail to adapt risk falling behind their competitors.
One of the primary advantages of warehouse automation is reduced errors. With manual inventory management, human mistakes can cause discrepancies in stock levels, leading to financial losses. Automated systems, on the other hand, can accurately track inventory levels, reducing error and ensuring that stock is always available when needed.
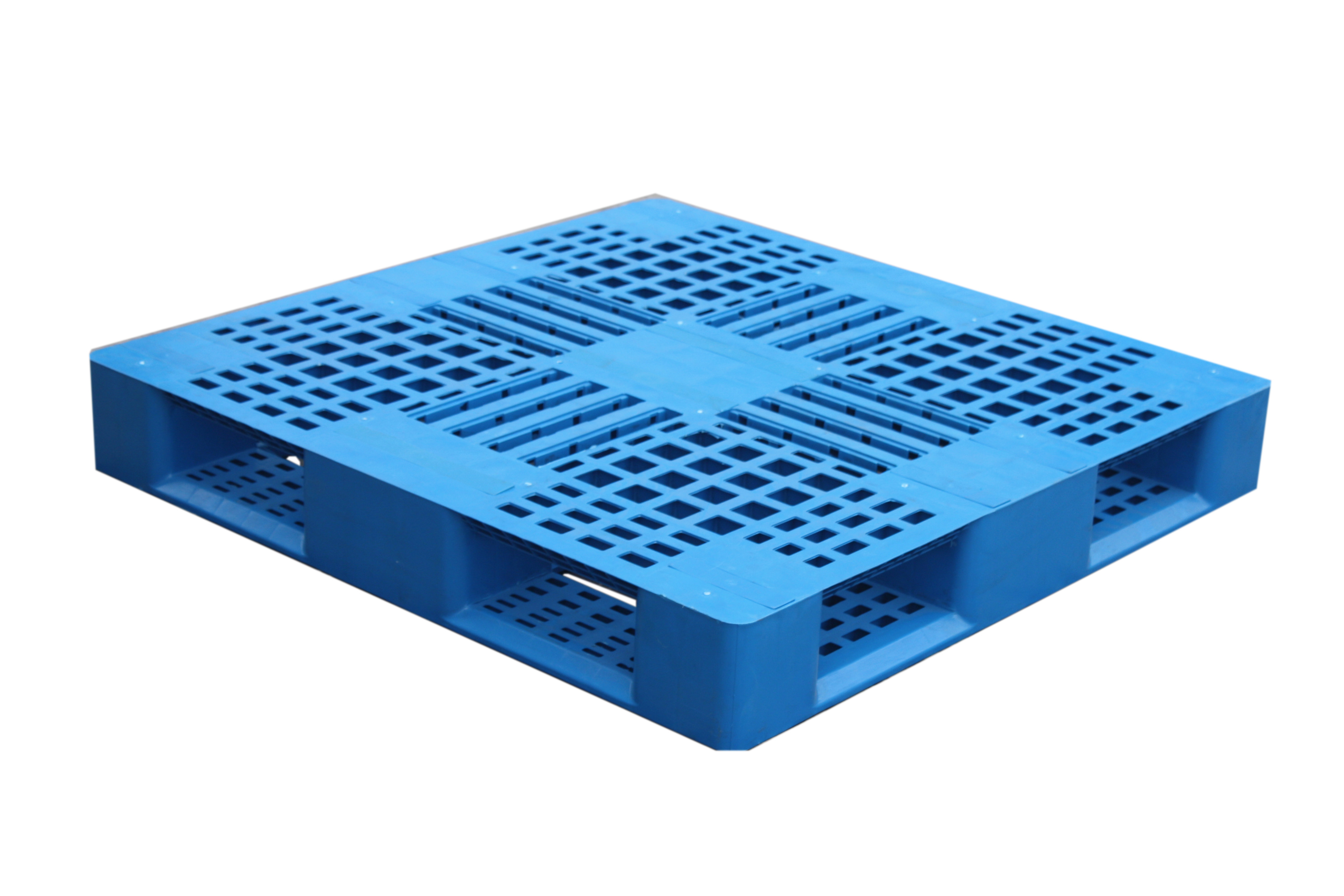
In addition to increasing accuracy and speed, warehouse automation can also help to reduce labor costs. By automating routine tasks, companies can reduce the need for manual labor, freeing up staff to focus on more value-added tasks. This can also help to improve employee morale, as staff are no longer burdened with unfulfilling tasks that can be automated.
To maximize productivity in your warehouse, consider implementing the following technologies:
1. Warehouse management systems (WMS): A WMS is the core of warehouse automation, providing a centralized platform for managing inventory, tracking orders, and automating tasks.
2. Automated storage and retrieval systems (ASRS): ASRS use robots and conveyor belts to store and retrieve inventory, reducing labor costs and increasing storage capacity.
3. Pick-to-light and プラスチックパレット pick-to-voice systems: These systems use lights or voice prompts to guide pickers to the correct products, reducing errors and increasing efficiency.
4. Automated conveyors and sortation: Automated conveyors and sortation systems can streamline the picking and packing process, reducing labor costs and increasing speed.
Implementation of warehouse automation requires a strategic. Here are a few key considerations:
1. Assess your current operations: Before implementing warehouse automation, it's essential to assess your current operations and identify areas for improvement.
2. Define your goals: Clearly define your goals and objectives for warehouse automation, including increased efficiency, reduced labor costs, and improved customer satisfaction.
3. Choose the right technology: Select the technologies that best fit your business needs, considering factors such as cost, scalability, and integration.
4. Train your staff: Warehouse automation requires a significant change in workflow and processes. Ensure that your staff are trained and equipped to work effectively with the new technology.
By following these best practices and implementing warehouse automation, companies can maximize productivity, reduce labor costs, and improve customer satisfaction. As the trend towards automation continues to grow, businesses that fail to adapt risk falling behind their competitors.
댓글목록
등록된 댓글이 없습니다.